Injection molding is one of those manufacturing technologies that is so central in our everyday lives that we hardly even notice its existence. It’s one of the most commonly-used plastic formation techniques with numerous industrial applications, and its market is continually evolving and expanding. Custom made plastic parts manufactured with injection molding are the perfect solution for multiple industries striving to produce a high volume of high-quality and cost-efficient parts.
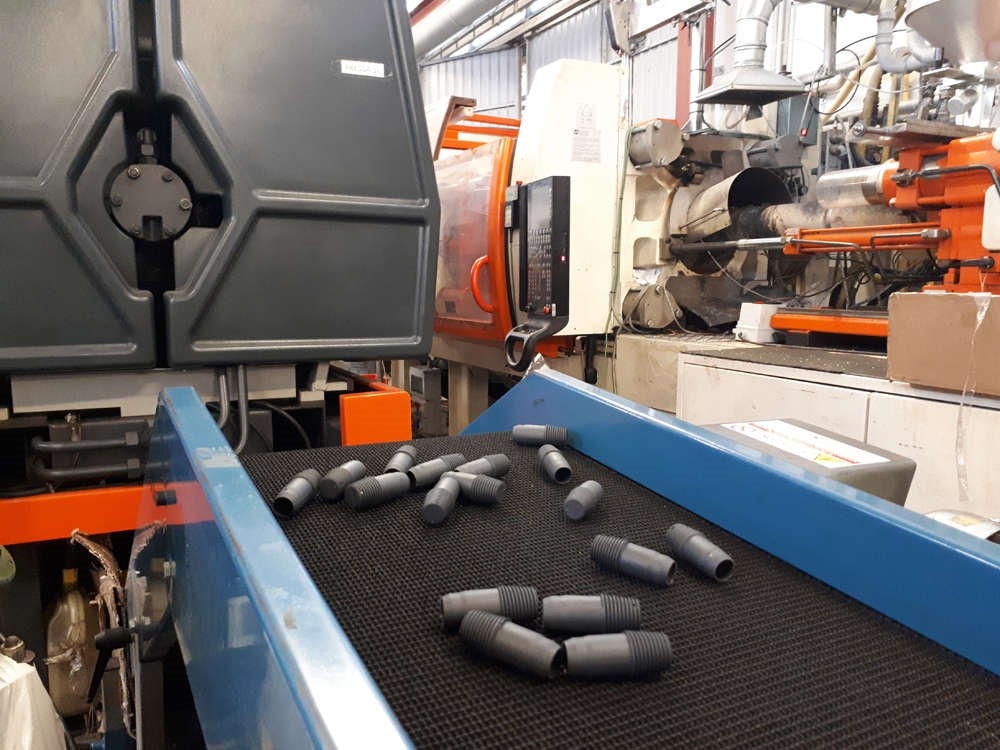
Healthcare represents the fastest-growing application segment for the industry. Pregnancy test devices, blood sample analysis cuvettes, and housings for needles are just a few of the preferred segments because of the lightweight, cost-effectiveness, and easy serializable properties of injection-molded plastic offers. As almost everything made from plastic is made with injection molding, the global injection molded plastics market size was valued at a staggering $258.2 billion in 2019, and it’s projected to grow further.
As a product designer who’s into injection molded products, it’s essential to understand this manufacturing process fully. Let’s get to it.
What Is Injection Molding?
Injection molding is a procedure that is used for manufacturing a wide variety of items from small components to large plastic parts. This technique uses a granular plastic that is gravity fed from a hopper, forced into a heated chamber by a screw-type plunger, melted, and then pressed against the mold. Later, the plastic cools and is removed as a solid part.
Rapid injection processes usually employ aluminum molds that are quick to make, while high-volume production typically uses steel molds. The injection molding cycle follows four crucial stages and usually takes between two seconds and two minutes to produce a part:
- Clamping. Clamping is the first part of the process where the two halves of the molds are closed by the clamping unit.
- Injection. Raw plastic material or plastic pellets are fed into the machine, pushed into the injection unit, melted, and afterward injected into the mold.
- Cooling. This phase allows the molten plastic to solidify and take the shape of the mold.
- Ejection. The ejection system is used when the plastic part is finished and is ready to be pushed out of the clamping unit.
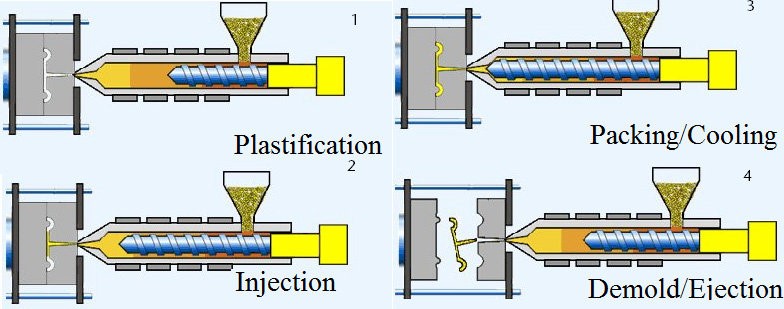
Benefits Of Injection Molding
Low Production Costs
With plastic injection molding manufacturing, the price per unit is relatively low. The most expensive costs are those for the setup of the operation. Once the initial costs of fabrication are paid, the profit margin can be quite significant. Injection molding makes financial sense in the business front, as long as there is a demand to satisfy the production.
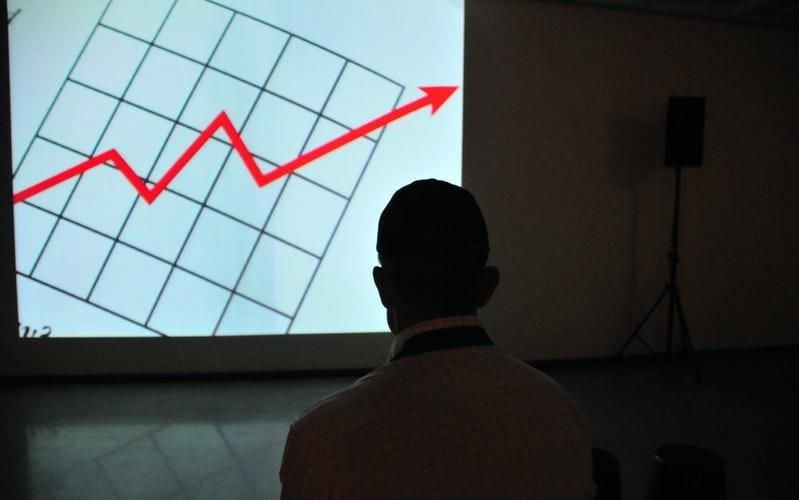
Repeatable And Consistent
Since injection molding is usually used in high-volume production, this manufacturing technique is ideal for producing practically identical parts and components. Each manufactured piece will be the same as the first one, which is vital for consistency and reliability.
The biggest challenge within injection molding is the design of the mold. Even though the main focus is mostly on the finished products, there would be no finished products made without the mold from which they are later formed. The design aspect of the mold is often overlooked, but it’s the essential part that guarantees repeatability and maximum consistency of the manufacturing process.
Low Scrape Rates
Unlike conventional manufacturing processes, where a considerable percentage of the original sheet or block is cut away during the production, injection molding cuts with precision, and the little waste plastic usually comes from excess material that leaks out of the cavities.
Important Design Considerations For Injection Molding
There are numerous aspects and factors to consider for injection molding, but the tool and part design are two of the most important. Getting them right could mean high production quality, shorter cycle time, lower entry cost, and quick assembly. On the other hand, getting them wrong could prove very costly, indeed.
Wall Thickness
One thing about injection molding is, the thinner the wall is, the easier the whole manufacturing procedure. Plastic parts with thin wall thickness weigh less, cool faster, and use less plastic per unit. This also means that the cycle time is shorter, resulting in more plastic parts produced per hour and lower production cost.
On average, injection-molded plastic parts should have a wall thickness from 2mm to 4mm, but thin wall injection can go as thin as 0.5mm. However, wall thickness dramatically varies and depends on the used material.
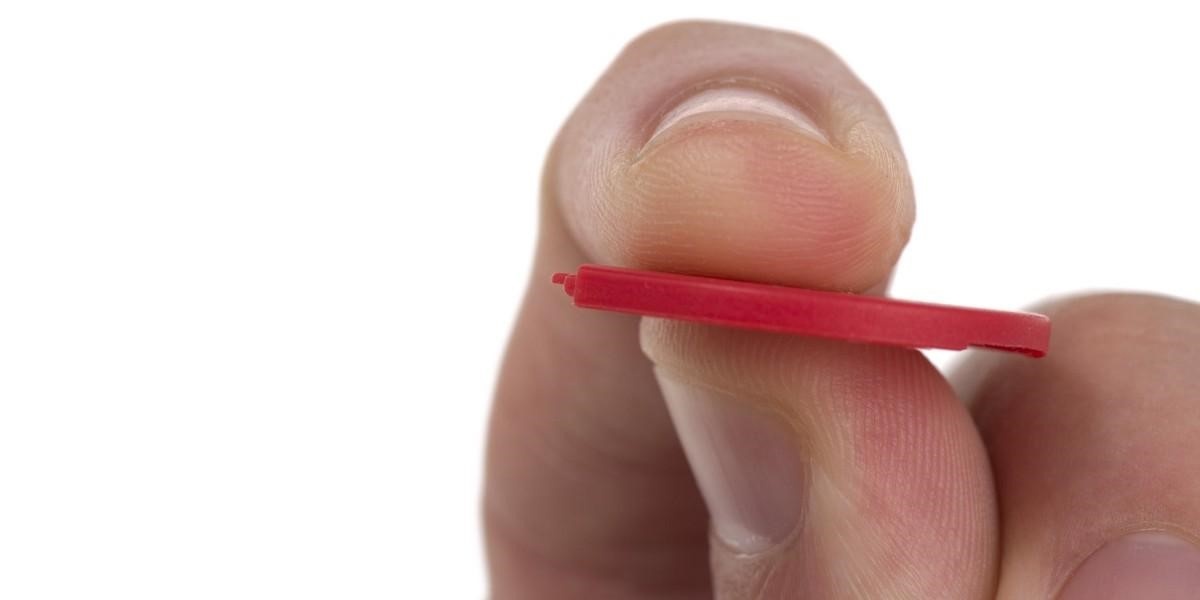
Ribs
Instead of growing the thickness of the wall, ribs are frequently used to enhance the bending stiffness of the plastic part, increasing in the moment of inertia. When adding ribs, make sure that the thickness of the ribs is no more than 60% of the nominal thickness, and the draft angle is at least 0.25°. Additionally, its orientation must be perpendicular to the axis where bending may occur, and the corners at the point of attachment must be well-rounded.
Bosses
Bosses are where fasteners like screws are attached, and they facilitate registration of mating parts. Decent bosses shouldn’t have thick sections that may result in sinking and voids. When designing the bosses of the injection-molded plastic parts:
- Ensure that the bosses’ wall thickness is no more than 60% of the main wall thickness.
- The bosses should be strengthened or supported by ribs connecting to the adjacent walls or ribs placed at the base.
- Ribs are a must to isolate bosses placed near a corner.
Final Words
Needless to point out, the injection molding manufacturing technique enjoys immense popularity and wide acceptance for a good reason. Injection moldings offer many benefits literally, making it the best manufacturing technique that can produce plastic parts and components that are precisely made, flexible, highly resistant, and cost-efficient.